- FläktGroup
- Solutions
- Pharmaceutical Cleanrooms
Pharmaceutical Production - Clean Room Ventilation
Producing pharmaceuticals requires a sterile environment and a very high level of cleanliness. Ventilation must provide the correct contamination & temperature control.
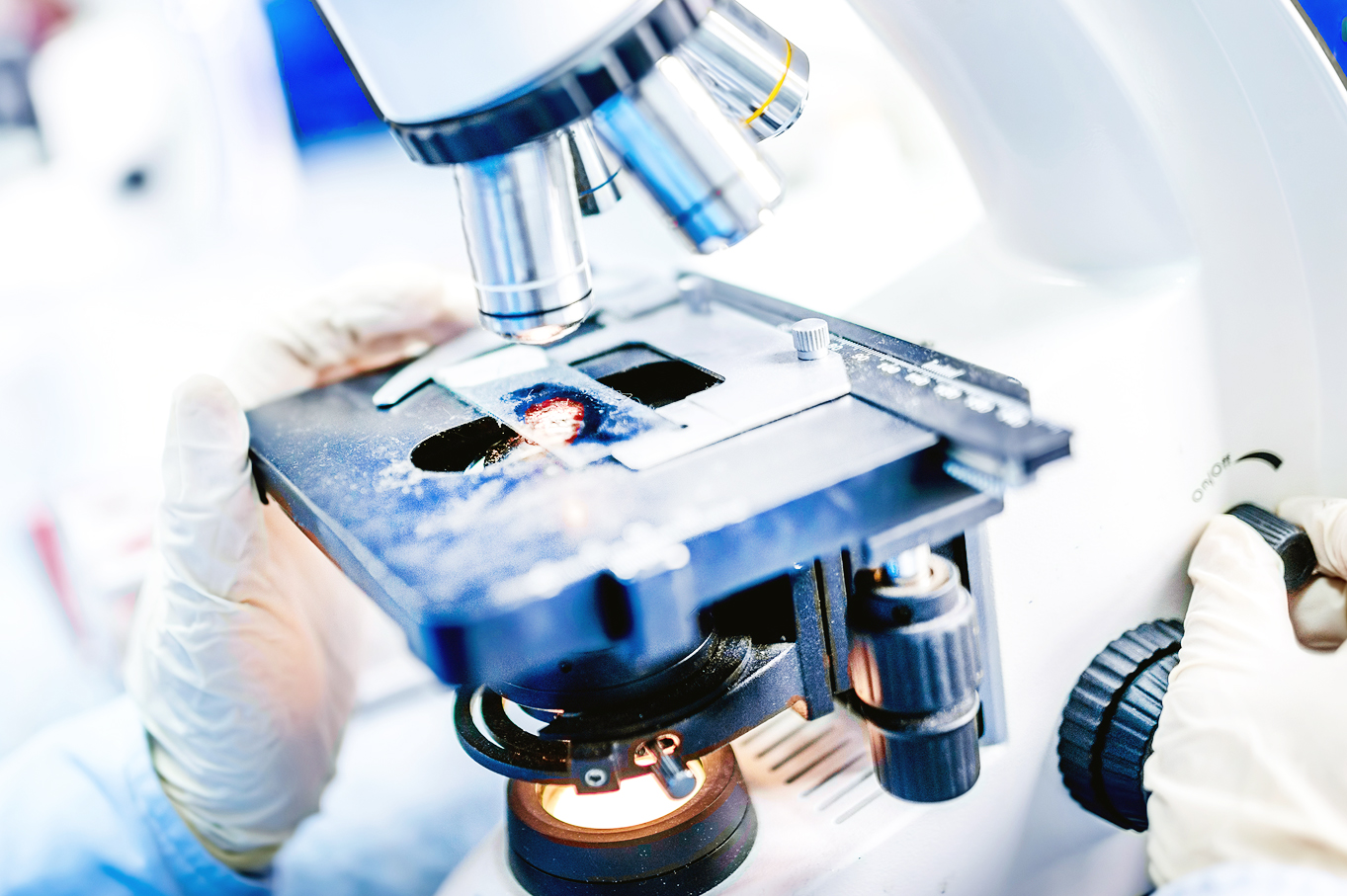
Safe and clean air for healthy lives
For both research and development, as well as mass production: whenever tablets are produced, liquids filled, substrates milled, estrogens or androgen substances produced, or health-endangering materials processed, air filtering is of critical importance.
Solid and liquid products must be protected from contaminants from ambient air. Employees must not be endangered and must be protected with extreme care: i.e., from inhaling toxic aerosols. And not least, the transmission of contaminated air into external areas must be prevented to avoid mutual contamination. Particles dissolved in the air, moreover, must be monitored and separated where they are produced.
Clean air solutions for a fast growing industry.
Biotechnology is a very fast growing industry that requires sterile air and equipment to maintain the required level of cleanliness needed when the main object of this industry is to modify living organisms to aid human purposes.
- Most processes are carried out in a controlled environment by utilizing clean rooms
- Very effective filtration of supply and exhaust air is necessary. A solution must be provide highly reliable ventilation and air management
Contamination Control
- Supply air needs to be filtered in three stages with a HEPA filter at the third stage
- Low turbulence airflow above the area with pharmaceuticals are exposed (almost laminar)
- Overpressure to the neighbouring rooms needs to be maintained at ca. 15Pa
- All surfaces inside of the room should be smooth and easy to clean – rounded corners, reduced numbers of joints
Temperature Control
Temperature control inside of clean and controlled environments is a very important topic. Attention must be paid to condensate-free cooling when inside a pharmaceutical production area, since any moisture that is brought in can become a culture medium.
- FläktGroup has vast experience creating clean air solutions for pharma production site
- Our full HVAC solution comes from a single source thus meaning installation is simple
- Full solution from FläktGroup guarantees increased synergies between all system components
- Requires highly efficient chillers and AHU’s specifically designed for such applications
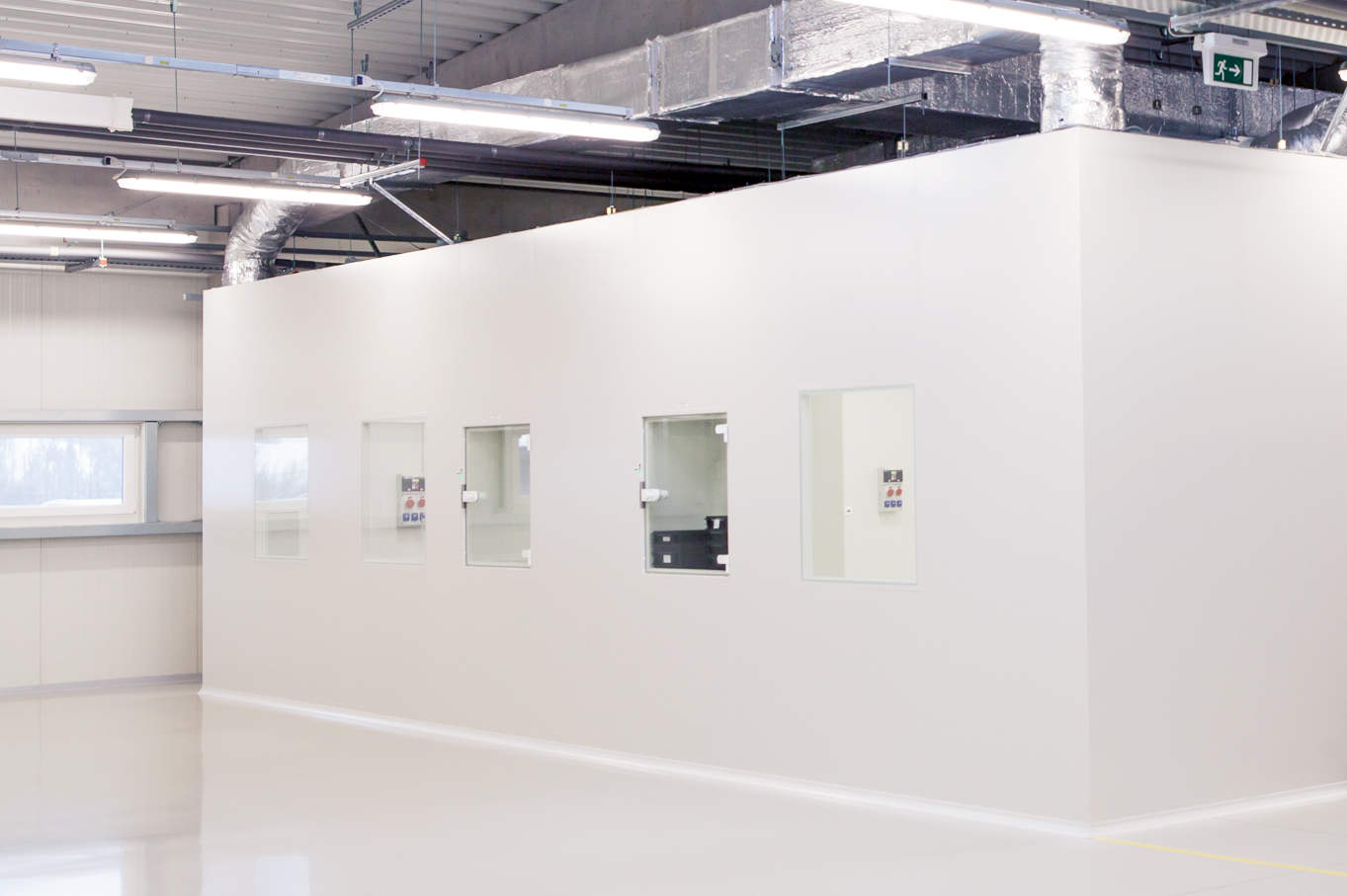
Clean Room Technology by FläktGroup
Numerous international manufacturers work with FläktGroup‘s Clean Room Technology as a result of our expertise in developing reliable and effective contamination control methods for Clean Rooms.
Clean Room services from FläktGroup permit users to coordinate all critical parameters precisely with the requirements of respective production processes and to systematically control decontamination of room air. These solutions control air pressure, temperature, and moisture – especially the contamination with fine dust, skin particles and bacteria – and keep these contaminants away from products and processes.
Effective and precise clean room HVAC design is essential for semiconductor production and pharmaceutical industries, as well as companies in the chemical industry, space technology, and optics and laser technology perform research and production; where we see that conditions in these industries are increasingly relying upon Clean Room conditions.
Technical, chemical, and biological quality products with highly sensitive manufacturing processes are further processed in hermetically sealed areas that demand room air that is virtually dust-free. The manufacturing process itself, however, requires ambient air absolutely free of particulates.
Our Process
We offer a full portfolio of support every step of the way from 3D design to installation, to reports in order to develop your bespoke project.
1. Consultation
With decades of experience in clean rooms, we bring the necessary expertise into your project and help you to create an optimal concept for the clean room, which is energy efficient and reliable.
2. Detailed Design
Once the clean room layout is finalized, we create a 3D model with all little details – to the last screw.
For you to check – and for our production.
3. Production
All our factories work with the 5S approach and have a best-in-class on-time delivery rate.
In our modern facilities we produce fast standardized products, but are flexible to support you with customized solutions.
4. Installation
The installation is a crucial part in the process. Especially for a clean room. Hence, we have very well trained teams in our core countries. Everywhere else, a supervisor from the factory will be present during the whole installation phase.
5. Validation
We support the finalization of your project by bringing in our long-term partners. You will get a full report, which is complying to all global and local regulations and standards. And – of course – you can be ensured, that your clean room will operate as required.
Products
-
SANDWICH PANELS
- The panels have a sandwich structure (two steel sheets with thermal insulation between them), with painted or stainless-steel sheet facing
- Custom colors and various core options are possible with minimal particle release
- R-panels 62 mm thick, M-panels and Me-panels are 60 mm thick
- Matching flush glassed-in panels (non-opening windows) and doors are available
- All joints are sealed by permanently elastic silicone in a color closely matching the panel color
- Round connections to the floor, suspended ceiling, and inner corners (Radius profiles system) are available
- The panels offer easy maintenance, effective sanitation, and resistance to disinfectants
- They ensure tightness to maintain over pressure or under pressure in the clean room
-
CEILINGS
- LS ceiling – clip-in light ceiling
- KS ceiling – grid cassette ceiling
- KSH ceiling – walkable Alucore grid ceiling
- RS ceiling – walkable sandwich panel ceiling.
- A minimum number of particles is released from the panel surface
- Ease of installation, cleaning and sanitation, resistance to conventional disinfectants
- Joints between cassettes are sealed using permanently elastic sealant
-
Inwall FACINGS
- The ideal solution for adapting existing rooms into clean rooms.
- Easy and quick fixation to structural walls
- All panels are prefabricated – minimal adjustments on site
- All joints sealed with silicone
- Panels connected via conductive cables are grounded to the earthing point
-
DOORS & WINDOWS
- An automatic drop-down seal integrated into the door leaf enhances the air-tightness of a door
- Being flush with sandwich wall partitions ensures easy maintenance and flawless disinfection
- An interlock system equipped with signaling units prevents both doors in an airlock room from being opened simultaneously, effectively reducing the risk of contamination
- Doors can be opened manually or automatically with automatic drive
- Transfer doors are used as partitions of transfer boxes (passive or with filtered airflow)
- Accessories available include automatic drives, door closers, mirrors, windows with sunblinds, windows made from float glass or safety glass (ESG, VSG), automatic drop-down seals, stainless-steel kick plates, electromechanical and electromagnetic locks, signaling panels (semaphore), and many more.
-
CGx Ceiling Air Outlet HEPA FILTER DIFFUSORS
- Used in pharmaceutical industry, laboratories, hospitals, microbiology, electronic industry, and food industry
- Easy integration in all types of FläktGroup suspended ceilings
- Filter classes H13 to U15 in an aluminum frame, with dry or fluid seal
- For turbulent displacement flow
- Integrated pressure-gauge connection for monitoring pressure drop
- Tube for applying test aerosol (measuring of concentration)
-
EXHAUST-AIR COMPONENTS
- Reliable ventilation of anesthetic gases, particles and exhaust of room air burdened with microbes
- Various choices of extract-air components
- Seamless integration of extract-air components in all types of wall panels and facings
-
Fresh Heaven MAXX LAMINAR AIRFLOW UNIT
- Size upon Customer’s demands
- Air delivered by AHU (FHM) or recirculation mode with power module (FHM P)
- H13, H14 or U15 filters with U-shaped or fluid gasket
- Casing in stainless-steel / steel in RAL 9010, height 450 mm (FHM) / 550 mm (FHM P)
- Various outlets (perforated stainless-steel / steel in RAL 9010, polyester fabric)
- Equipped with autonomous automatics (local control via Siemens LOGO! panel)
-
CAIRplus AIR HANDLING UNIT
- CAIRplus is the tailor-made premium range of modular air handling units for every customer requirement
- Environmentally-friendly design means an energy recovery system with high efficiency is available for every configuration
- Clean surfaces and ease of cleaning guarantee hygienic standards to VDI6022
- All units can be supplied with FläktGroup integrated controls ISYteq 4.0
- T2/TB2/L1/D1 Eurovent certified casing
-
GLFC 2150-2600 DA2 (286 - 1212 kW)
- Version with 2 screw compressors
- SEPR-HT values up to 6.3
- ErP 2021 compliant with EU 2016/2281
- Available as Standard or Super-Low noise (SL) versions
-
eQ MASTER® AIR HANDLING UNIT
- Tailor made for customer needs
- Energy Efficient and optimized with integrated control
- Large variety of high efficiency components
-
EHSD CIRCULAR FLOW VARIATOR
- Easy and Quick Selection
- Insulated casing
- Integrated orifice plate for air measurement
- FG compact controller as standard